Implanter les 30 outils du Lean Management en coopération avec ceux qui les utilisent
Le Lean Management s'appuie sur une palette d'outils et de bonnes pratiques qui ne sont utiles que si et seulement si on les implante en coopération avec tous ceux qui devront les utiliser. Sinon, ce n'est pas compliqué, au mieux ça marche très mal et ils sont rapidement abandonnés, au pire ils sont utilisés en dépit du bon sens. Voyons comment s'y prendre pour chacun des 30 outils et bonnes pratiques sélectionnés ici...
L'article résumé en quatre points clés...
- 1. Sans une réelle coopération, on ne progresse pas en harmonie. Cela devrait tomber sous le sens et c'est dommage de devoir encore le répéter. L'autoritarisme n'est pourtant pas la solution, tant s'en faut, pour inciter les créateurs de valeur que sont les salariés à faire preuve d'initiative. Pour produire de la qualité sans se limiter au respect "robotisé" des procédures, encore faut-il s'approprier les outils, méthodes et bonnes pratiques. Et c'est uniquement avec une approche coopérative que l'on y parviendra. Voir ici la méthode pour conduire le projet Lean en coopération
- 2. Ensuite, avec un peu de réflexion "hors du cadre", on découvre rapidement que l'usage de ces outils et bonnes pratiques ne se limite pas à la seule course à la productivité comme il est de coutume de les associer.
- 3. On peut justement réfléchir à une définition de la performance plus englobante accordant la priorité au bien-être des créateurs de valeurs que sont les salariés et pour une fois sans se lancer dans les contes à dormir debout des vendeurs de bonheur au travail et autres supercheries.
- 4. Commençons par un rappel historique bien nécessaire avant d'étudier les 30 outils et bonnes pratiques.
L'origine des outils et bonnes pratiques du Lean
Les inventeurs du
lean Management ou pour être plus juste, les fondateurs du Toyota Production System, ont su fédérer un ensemble d'outils et de bonnes pratiques pour assurer une production de qualité avec maîtrise des coûts et des délais.
Pour la petite histoire, il est bon de savoir que le succès de l'automobile Toyota, qui s'appelait alors Toyoda du patronyme de ses fondateurs, ne s'est pas fait tout seul, tant s'en faut.
Un urgent besoin d'outils "qualité"
Experts et innovateurs de premier plan pour la fabrication de métier à tisser automatique, lorsque la famille Toyoda a pris le virage de la fabrication automobile pour concurrencer "Géneral Motors" notamment qui marquait des points au Japon,
ils rencontrèrent d'énormes problèmes de qualité.
Par exemple, en fonderie, 8 cylindres sur 10 étaient bons pour la benne ! (Source Toyota Commemorative Museum of Industry and Technology Nagoya Japan) Ce n'était pas tenable. Il fallait trouver une solution : la mesure.
La mesure au coeur de la démarche
Kiichiro Toyoda fils du fondateur
Sakichi Toyoda, est l'initiateur du virage à la fabrication automobile pris l'entreprise familiale. Il ne s'en est évidemment pas tenu là. Le groupe a rapidement mis la qualité au premier plan et adopté des principes rigoureux sans s'en tenir au
Jidoka qu'ils maitrisaient déjà de longue date pour la fabrication des métiers à tisser.
Bien évidemment, la démarche qualité, quelle qu'elle soit, ne peut se passer de la mesure. Un point qu'avaient parfaitement compris les ingénieurs de Toyota à ce stade.
Plus tard, au fur et à mesure des expériences de terrain et des initiatives des ingénieurs tels que Taiichi Ohno, les outils et bonnes pratiques décrits ci-après se sont ajoutés et intégrés dans le système de gestion industriel que l'on connait aujourd'hui (Toyota Production System et Lean Manufacturing).
Les 30 outils incontournables du Lean et plus généralement de l'organisation industrielle
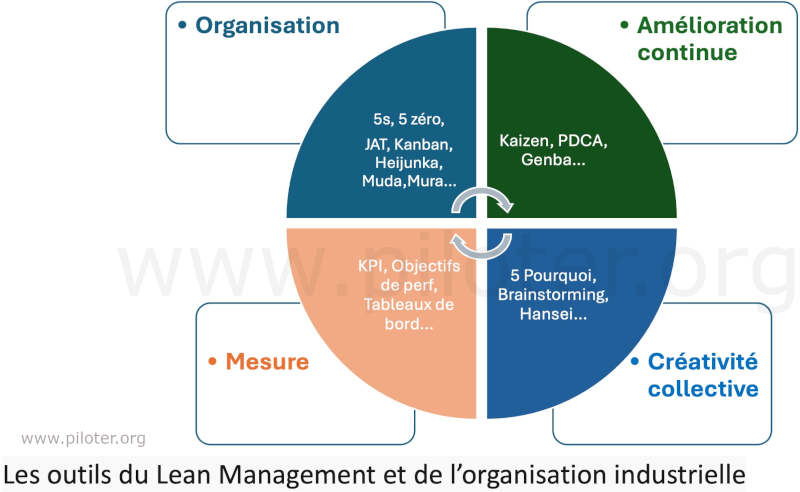
Légende : Les outils du Lean et de l'organisation industrielle classés en 4 catégories.
Passons-les en revue. Ils sont ici classés selon 4 thèmes :
1) Bonnes pratiques et méthodes dédiés aux préoccupations organisationnelles
5 S
Les 5S sont les initiales en japonais des cinq opérations de base indispensables pour rationaliser les tâches :
Seiri Débarrasser, Seiton Ranger, Seiso Nettoyer, Seiketsu Standardiser, Shitsuke Discipliner & Éduquer. Ces cinq recommandations, pour ne pas écrire ces cinq injonctions quand on voit sur le terrain comment elles sont imposées par les ultra-rigoristes du Lean, s’envisagent dans un esprit d’amélioration continue. Elles devraient devenir, dans l'esprit Lean, une habitude pour tout un chacun.
Pourtant, ce n'est pas une fin en soi et avant de l'imposer tous azimuts il est préférable d'en discuter avec les personnes concernées.
5 Zéros + le zéro mépris
Le concept des 5 Zéros est quelque part le fondamental du toyotisme :
Zéro défaut, Zéro papier, Zéro panne, Zéro stock, Zéro délai. C'est en effet sur ce principe que se construisent le Juste à temps et le Kanban et par extension les
démarches qualité. Il est toutefois dommage d'omettre un sixième zéro à cette liste :
le Zéro mépris sans quoi rien n'est possible puisque le progrès repose justement sur les femmes et les hommes "d'en bas", ceux qui en fait créent la valeur.
Autonomation
Selon
Taiichi Ohno, il faut s'efforcer d'exploiter les machines pour simplifier le travail des hommes. Pour cela, il s'agit d'aller plus avant de la simple automatisation pour donner de l’autonomie à la machine comme le sous-entend le terme d'autonomation. Dans la mesure du possible,
la machine automatisée doit aussi prévenir les erreurs et les défauts de fonctionnement et les corriger si possible tout en préservant l’opérateur des accidents.
Benchmarking
Cette démarche vise à évaluer la performance des processus d'une entreprise ou d'un service, comparativement à un autre service, une autre entreprise du groupe, un partenaire ou un concurrent jugé comme référent.
L'idée est dans définir des "bonnes pratiques" une fois que l'on a précisé une métrique.
Ce dernier point est ultra important. C'est cette métrique qui permettra d'apprécier la "bonne pratique" potentielle afin de s'assurer qu'elle peut être transposée dans l'entreprise sans générer trop de coûts et de contraintes. la bonne méthode c'est justement de mettre de côté ses réactions binaires et subjectives (Wahou! Trop génial ! Il faut que l'on fasse pareil !) pour s'en tenir aux critères objectifs.
Bref, la métrique bien choisie, bien étalonnée, bien en phase avec la problématique fait toute la différence.
Cadence de production
Réduire les délais entre la prise de commande et la livraison au client nécessite une augmentation de la cadence de production. Pour ce faire, les organisateurs ne disposent pas de 36 méthodes. Quel que soit la cosmétique autour de la démarche, elle se traduira pratiquement systématiquement par
un accroissement de la pression sur les individus au travail.
Remarque : C'est ce que l'on appelle dans l'article explicatif "Augmentez les cadences !" la méthode "Brut" et ses variantes. Ce n'est pourtant pas la seule approche, et nous poursuivrons par une réflexion sur l’optimisation des flux bien souvent aussi opportune qu'efficace.
Heijunka
Le Heijunka est une démarche visant à lisser la production, la niveler, pour éviter autant que faire se peut les changements de série intempestifs. Il s'agit d'être moins obsédé par la fabrication à la commande proprement dite et d'anticiper un tant soit peu sur un laps de temps donné.
Nécessairement, sur un horizon de temps court, les commandes clients ne sont pas régulières. Si on colle étroitement la production à la commande, elle ne sera évidemment pas régulière.
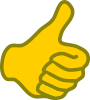
En revanche, si on se base sur un horizon de temps un peu plus long, on peut procéder à une manière de regroupement des commandes pour rendre la production plus régulière, sans à-coups, et c'est cela que vise le Heijunka pour mieux stabiliser le processus.
Jidoka
L'idée, c'est de réduire la variabilité des processus afin d'éviter, notamment, que des non-conformités se retrouvent chez les clients. En fait, il s'agit de produire "bien" du "premier coup". Il ne faut donc pas causer d'erreurs. Un des principes les plus simples du Jidoka est le fait d'arrêter la machine automatiquement dès qu'une erreur se produit.
Pour la petite histoire : Le JIDOKA était déjà utilisé pour la fabrication des métiers à tisser du temps de Sakichi Toyoda, fondateur de la "dynastie" et génial inventeur, entre autres du JIDOKA.
Au moindre problème survenant lors du processus de production, le système Toyota de détection automatique d'erreurs (Jidoka) donne l'alarme et permet ainsi aux employés sur la chaîne de prendre les mesures nécessaires pour le résoudre sur place - même s'il faut pour cela interrompre la production.
Source : le site Toyota.
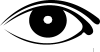
On parlera de
"autonomation", un mot-valise construit à partir des deux substantifs:
"autonomie" et
"automation". Autonomation vise à prévenir la survenance de défauts par un principe "d'automation intelligente", toujours au service de l'humain.
Différenciez les tâches qui peuvent être exécutées par les humains de celles qui peuvent être réalisées par des machines. N’utilisez pas les humains comme gardiens des machines, assignez-les plutôt à des tâches qui ne peuvent être réalisées que par des humains.
Taiichi Ohno
Propos rapporté par Yoshihito Wakamatsu : lire: The Toyota Mindset, The Ten Commandments of Taiichi Ohno, Routledge, 2017
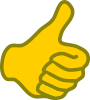
On parlera aussi dans la même logique de
Poka Yoke et on s'intéressera de même à
l'AMDEC pour bien identifier les risques potentiels de défaillance.
Juste à Temps
L'idée du
JAT Juste À temps (JIT Just In Time), c'est de produire au juste moment uniquement ce qu'il faut.
Quand il faut, ce qu'il faut, comme il faut.
Au lieu de "pousser" la fabrication en se basant sur des prévisions de ventes plus ou moins précises, on "tire" la fabrication depuis la demande client.
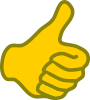
Ainsi, on réduit drastiquement les stocks et le nombre d'encours (WIP, Work In Progress, Work In Process) pour conserver uniquement ce qui est nécessaire à la fabrication des articles commandés par le client, et le livrer au juste moment.
"Kanban"
La démarche Kanban est le moyen de réaliser un système de production organisé en Juste à Temps, en flux inversé.
La production est "tirée" par la demande client, et chaque poste de travail du processus est client du poste qui le précède.
Ainsi, c'est le poste en aval qui demande des approvisionnements au poste en amont à l'aide justement d'un "Kanban". Ce terme japonais désigne l'étiquette comportant les quelques instructions indispensables pour réaliser la commande.
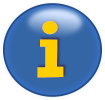
Voir ici pour plus de détails :
Kanban.
Muda
"Muda" désigne un premier type de gaspillage. Tout ce qui coûte inutilement et doit impérativement être éliminé. On peut citer les temps d’attentes, les déplacements redondants, les stocks inutiles et même la surproduction.
Passons en revue les sept sources de gaspillage selon la synthèse proposée par Taiichi Ohno
1) Surproduction
Surproduire, c'est produire plus qu'il ne faut pour le client et créer du stock invendu pour utiliser les ressources ou anticiper les commandes à venir. À l'origine de ce comportement tient le dimensionnement des lots de production. Les temps de changement d'outils et de réglages sont longs. Pour cela, il existe des techniques telles que SMED (Single-minute Digit exchange of die).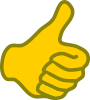
Prendre soin de considérer tous les paramètres pour bien dimensionner la taille des lots selon les commandes à servir.
2) Stocks excessifs
Les stocks sont, la plupart du temps, les cache-misères des processus de production non optimisés. Ils servent en effet à pallier des dysfonctionnements techniques ou humains. Réduire les stocks, impose de bien comprendre l'importance de la régularité des flux. En contrepartie, le zéro stock met une pression supplémentaire sur les hommes de la production qui ne disposent plus de roue de secours en cas de dysfonctionnement indépendant de leur volonté.
3) Défauts, retouches et rebuts
S'efforcer de faire bien du premier coup, soigner les procédures. On rejoint là le JIDOKA.
4) Temps d'attente
Un processus efficace est nécessairement fluide... Attention aux goulets d'étranglement.
5) Transports inutiles
Il s'agit d'optimiser les emplacements des lieux de production.
6) Déplacements inutiles
Rationalisation des mouvements et déplacements.
7) Traitements inutiles
Éviter les travaux inutiles pour la valeur créée. Toute la question de la surqualité se pose aussi à ce stade.
Et ne pas oublier la huitième source de gaspillage :
la sous-utilisation des compétences. C'est une perte sèche autant pour l'entreprise que pour le salarié. C'est une cause majeure de démotivation. Cette source de gaspillage n'est pas toujours la plus aisée à identifier.
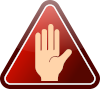
Un bémol toutefois, il est toujours préalable de s'assurer que le salarié souhaite exploiter l'ensemble de ses compétences. D'expérience, ce n'est pas une généralité. À voir au cas par cas. D'où l'intérêt de toujours discuter avant de décider.
Mura
"Mura" désigne un deuxième type de gaspillage. Toutes les formes d'irrégularités dues le plus souvent à un manque de standard et, plus généralement, tout ce qui est susceptible d'entraver la régularité des flux.
Muri
Ce terme désigne un troisième type de gaspillage. Il s'agit de toutes les formes de démesures. Ce peut être l’utilisation de moyens de production ou d'outils surdimensionnés pour la tâche à réaliser. Ce peut être aussi la pénibilité, le stress, les efforts déraisonnables ou une surcharge de travail continue pour ceux qui doivent l'exécuter. En fait, le terme "Muri" désigne toutes les formes d’excès que l'on peut restreindre, notamment en développant la standardisation et l'ajustement du
Takt Time.
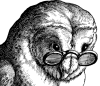
Quand la production s'emballe
Il est cependant prudent de se laisser des marges de sécurité afin d'absorber les éventuels sursauts de production. Autrement dit, glisser au besoin un peu de
"Slack", c'est-à-dire du "mou", dans les processus pour éviter de trop mettre la pression sur les hommes et les équipements.
Toutes les productions ne sont pas régulières, tant s'en faut, et donc difficiles à lisser définitivement. Il faut aussi savoir adapter les outils et méthodes à la réalité de la situation. Dans cet esprit, il est tout aussi prudent de bien savoir interpréter le TRS, Taux de Rendement Synthétique, pour éviter de bâtir des systèmes de production surtendus où le moindre aléa met en péril le processus.
Poka Yoke
Le
poka yoke est une méthode pour prévenir les erreurs d'utilisation dès la conception des produits, à la manière d'un détrompeur. Attention toutefois de ne pas chercher à l'étendre au management sans prendre quelques précautions.Notamment lors de l'établissement des procédures, il s'agit de ne pas prendre les autres pour des imbéciles en verrouillant toutes possibilités d'initiatives opportunes.
SMED
SMED pour "Single Minute Exchange of Die" est une méthode destinée à ne pas perdre de temps à régler les paramètres de production lors des changements de série. L'idée est donc de s'organiser pour
changer d'outils rapidement et d'optimiser les réglages afin qu'ils soient le plus simple possible entre chaque changement de série.
Standardisation
La standardisation poussée à son extrême est le point clé du toyotisme et par extension du Lean Management. C'était déjà le point fondamental du taylorisme puis du fordisme. Taiichi Ohno pousse encore plus avant ce concept afin de mieux exploiter les "bonnes pratiques" mises au point dans les ateliers.
Tout repose ensuite sur la qualité de conception des procédures définissant la manière d'exécuter le travail à réaliser. Pour cela, il s'agit de bien confronter la faisabilité des procédures en se rapprochant au plus près de la réalité du travail sur le terrain (voir le Gemba).
Ensuite, au fil du temps, la procédure évolue, s'améliore, c'est aussi à cela que sert le Kaizen.
Remarque personnelle : Voir l'article humoristique malgré lui : Bien des concepteurs de procédures devraient s'inspirer de cette démarche pragmatique...
En pratique, les procédures et modes de travail sont établis par des prescripteurs qui se tiennent loin de la réalité et ne jurent que par "la méthode". En fait, ils appliquent des "recettes".
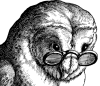
Il en est de même pour les trop fameuses "bonnes pratiques" qui sont sélectionnées par ces mêmes prescripteurs, sans se préoccuper du point de vue de ceux qui seront en charge de les appliquer.
Une bonne part du drame du management moderne est justement due à cette distance entre ceux qui prescrivent et ceux qui doivent appliquer des consignes inadaptées. Le
mépris évident des prescripteurs envers les exécutants explique cela.
Takt Time
Ce terme d'origine germanique définit le temps idéal au sens du client de réalisation d'une tâche. Il est utilisé pour dimensionner une chaîne de production. Imaginons un client qui achète 1000 pièces par jour. Pour soutenir ce rythme, il faut donc que toutes les activités du processus soient à même d'assurer le débit.
C'est à cela que sert le Takt Time : à dimensionner le flux du processus.
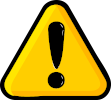
Ce paramètre n'est pas équivalent au
"Temps de Cycle" qui, lui, définit le temps réel d'exécution d'une tâche précise, indépendamment du client. Idéalement, le Temps de Cycle doit être au plus près du Takt Time. Si le Temps de Cycle est supérieur au Takt Time, on ne parviendra jamais à assurer la commande, s'il est inférieur, on est en surcapacité.
2) Bonnes pratiques et méthodes dédiés à l'amélioration continue
Gemba
Le Lean vise à mieux servir le client, tout en améliorant drastiquement la rentabilité. Pour y parvenir, l'idée du Lean est justement de mobiliser les acteurs de l'entreprise, surtout les cadres dirigeants à descendre sur le terrain, là où l'on conçoit, la où l'on produit, là où on livre...
C'est logique.
Qui connait mieux son environnement de travail que celui qui y passe huit heures par jour, cinq jours sur sept à créer la valeur ? Ce sont eux qui détiennent la clé des améliorations.
Donc, c'est sur le terrain que l'on peut identifier les problèmes et envisager les solutions d'amélioration. Ce n'est pas dans des bureaux distants, loin de là où se crée la valeur, c'est cela le Gemba (ou genba).
Gemba Walk
C'est justement une incitation adressée aux membres de la direction de l'entreprise à descendre périodiquement sur le terrain, dans les ateliers pour regarder, écouter, questionner et apprendre comment se créer la valeur.
Ils seront accompagnés à l'occasion d'un expert du Lean, un "sensei".
Quand vous êtes en phase d'observation sur le "Gemba", faites quelque chose pour aider ceux qui travaillent là. Si vous le faites, les hommes prendront conscience que vous pouvez les aider et seront pressés de vous revoir sur le Gemba. Taiichi Ohno
En réalité, ç se passe comment ?
Il est vrai que sous nos tropiques, les seuls "voyages sur les lieux de création de la valeur que la direction s'autorise, c'est toujours au titre d'une visite client ou d'un prospect important. Ce n'est jamais pour chercher à comprendre justement le
processus de création de valeurs et apprécier l'apport indiscutable des salariés à la production de richesse.
Quant à leur demander comme le suggère Taiicho Ohno de faire quelque chose pour eux, c'est le plus souvent mission impossible puisqu'ils n'ont aucune idée de la difficulté des tâches à exécuter, des compétences requises et des efforts fournis et que cela ne les intéresse guère.
Bon, il existe des exceptions, bien évidemment. J'en ai croisé qui avaient monté leur boîte de pas grand-chose et savaient très bien comment elle fonctionnait. Malheureusement, ils ne représentent pas la majorité des dirigeants et statistiquement on peut généraliser sans risques.
Quelque part, c'est aussi cela le mépris déjà évoqué ci-dessus au paragraphe
5 zéros.
Chantier Hoshin
Chantier Hoshin (Hoshin Kanri) que l'on dénomme aussi à l'occasion Kaizen Blitz est une
démarche d'amélioration orientée vers un objectif bien précis. Littéralement, « Hoshin » signifie « direction », tandis que « Kanri » signifie « gestion » (source : toyota-forklifts.be). Hoshin Kanri précise la démarche collective et fédérée de tous les employés concernés pour accéder à l’objectif à moyen terme de l’entreprise.
Bien évidemment, il s'agit au préalable de concevoir une stratégie claire, compréhensible et largement diffusée auprès des intéressés afin de pouvoir la décliner en objectifs.
Lesdits objectifs doivent impérativement être fédérateurs si l'on espère mobiliser les salariés pour les atteindre. C'est un préalable. Impliquer les salariés concernés dans le choix des objectifs, comme le préconise depuis près de trente ans la
méthode Gimsi, semble une évidence qui pourtant est loin d'être acquise.
Dans l'entreprise, on préfère toujours imposer plutôt qu'impliquer. C'est ainsi.
En pratique, le Hoshin Kanri se focalise sur un objectif prioritaire et cherche à l'atteindre le plus rapidement. C'est aussi pour cela que certains traduisent cette démarche par "Kaizen blitz". Classiquement, en tout quand dans l'esprit TPS, la démarche se fonde sur le
PDCA, Planifier, Executer, Vérifier et agir en conséquence, symboliser par la fameuse roue de Deming matérialisant non seulement la répétabilité des 4 phases de la démarche, mais aussi l'importance de l'expérience acquise pour ne pas revenir en arrière.
Même si l'on traduit parfois le Hoshin Kanri par Kaizen Blitz, il est prudent de ne pas confondre les deux démarches.
Pour plus d'information, voir le site de la
revuegestion.ca (HEC Montréal) qui précise assez bien les phases et les attendus de la démarche.
Kaizen
Ce terme désigne ce que l'on pourrait appeler une
philosophie de l'amélioration continue. Il s'agit de résoudre les problèmes inhérents à toutes activités, de développer des solutions opérationnelles, d'optimiser au mieux les processus de fabrication, de perfectionner ce qui peut l'être et ce qui doit l'être, bref d'améliorer en continu, sans brusquerie, mais toujours dans un mode coopératif.
Il faut reconnaître que le Kaizen est réellement un excellent d'outil d'amélioration. Et si on réfléchit un tant soit peu, on prend vite conscience que l'on peut utiliser le kaizen tout comme le PDCA sans se limiter à une recherche de standardisation dans la seule dimension de quête infinie d'amélioration de la productivité.
Le Kaizen se révèle un excellent outil pour améliorer drastiquement les conditions de travail.
Encore faut-il aller au-delà des promesses des vendeurs de salades du lean, dignes d'un futur élu politique en période de serrage de mains sur les marchés avant une élection majeure pour sa carrière... On en parle
ci-après et c'est le sujet de mon dernier livre présenté en bas d'article.
PDCA
Le PDCA, pour Plan ➔ Do ➔ Check ➔ Act, est représenté par la fameuse Roue de Deming pour matérialiser les 4 étapes à enchaîner dès qu'il s'agit de résoudre un problème, de progresser : Planifier, Faire, Vérifier, Agir. Et l'on reboucle jusqu'à parvenir à solutionner le problème, à atteindre l'objectif fixé.
3) Instruments dédiés à la mesure et au pilotage de l'amélioration continue
Indicateur de performance
Un indicateur de performance, KPI en anglais, est
l'instrument clé de toutes démarches d'amélioration. L'
indicateur de performance judicieusement choisi en équipe va servir non seulement à mesurer son avancement sur l'échelle du progrès, mais aussi à s'assurer que l'on est dans la bonne direction et que l'on a adopté le bon rythme. C'est dire si le processus de
choix des indicateurs est une étape primordiale du projet.
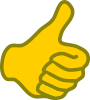
Bien entendu, il faudra plusieurs KPI pour remplir un tel office. Ils seront regroupés sur un
tableau de bord.
Objectif de performance
La principale difficulté rencontrée par tous ceux qui s'engagent dans une démarche d'amélioration continue est le
choix d'un objectif de performance concret, réaliste et fédérateur. Un objectif de performance ne s'impose pas. Si on n'accorde pas foi en sa pertinence, s'il n'est pas motivant, il ne servira pas. C'est ainsi que ratent les démarches de progrès, qu'elles soient
Kaizen ou pas.
Tableau de bord
Le tableau de bord n'est pas qu'un présentoir d'indicateurs et de ratios. Un tableau de bord est structuré afin d'être
cohérent et passer ainsi le "sens" de l'information. Un tableau de bord se compose selon des règles précises.
On ne s'attarde pas plus longtemps sur ce thème puisque c'est un des thèmes principaux de ce site d'informations gratuites pour managers.
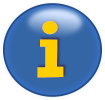
Voir ici le dossier complet :
Comment réaliser le tableau de bord.
4) Outils et bonnes pratiques dédiés à la résolution de problèmes et à la créativité collective
Les 5 Pourquoi
Les 5 Pourquoi est
une méthode de résolution des problèmes qui permet de ne pas se contenter de la première cause apparente, mais bien de se questionner afin de remonter à la vraie cause initiale. À chaque nouvelle étape de la réflexion, on se pose la question "Pourquoi ?" afin de remonter encore plus avant en amont et atteindre ainsi la cause originelle sans se contenter d'un traitement symptomatique du problème.
Remarque : La méthode des 5 Pourquoi ne se limite pas à la méthode Lean ni à la production industrielle. Elle est utilisable pour bien des domaines d'activités. Il est tout aussi utile de s'intéresser à la sélection des outils de résolution de problèmes et de créativité collective.
Brainstorming
Le brainstorming, littéralement tempête de cerveaux ou remue-méninges, est une
méthode participative de résolution de problèmes s'appuyant sur la créativité spontanée des participants. En fait, c'est bien la spontanéité qui est recherchée. Voyons la démarche ou plutôt le protocole à suivre si l'on souhaite parvenir à un résultat.
Diagramme d'affinité
Le
diagramme d'affinités est un outil bien pratique pour fédérer les idées d'un groupe et parvenir ainsi à un consensus actif. C'est bien entendu un outil de créativité collective. Aisé à mettre en oeuvre, il est cependant important de bien suivre le processus à la lettre.
Diagramme d'Ishikawa dit causes-effets
Le
diagramme causes-effets d'Ishikawa, en référence au patronyme de son concepteur promoteur aussi appelé diagramme arête de poisson en raison de sa graphie, est un outil qualité utilisé pour identifier les causes d'un problème.
Le diagramme Ishikawa est aussi fort utile pour tout autre type de réflexion fondé sur l'identification du cheminement causes effets. Comme pour la large majorité des outils dédiés à la résolution de problèmes, le diagramme d'Ishikawa nécessite pour sa réalisation et sa pleine utilisation une démarche coopérative et engagée de toutes les personnes concernées de près comme de loin par la résolution du problème en cours.
Hansei
Hansei (autoréflexion) est une manière d'autocritique afin de mieux intégrer sa capacité toute naturelle à commettre des erreurs. L'analyse des erreurs, tout comme la reconnaissance de les avoir commises, est partie intégrante de l'amélioration continue.
Encore faut-il ensuite trouver le juste milieu entre l'auto-culpabilisation et l'autocritique façon procès soviétique avec le bannissement à la clé !
En fait, tout dépend du principe de relation existant dans l'entreprise entre les individus, tout comme du degré de droit à l'erreur consenti.
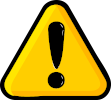
Attention, sans une réforme culturelle de l'entreprise fondée sur le respect des uns et des autres, l'exercice du Hansei peut se révéler pour le moins périlleux.
QQOQCP Qui Quoi Comment...
Se poser ces sept questions :
Qui Quoi Où Quand Comment Combien Pourquoi", résumé avec le sigle QQOQCCP ou 5W 2H, et répondre précisément à chacune d'entre elles sans faux fuyants est la meilleure méthode pour s'assurer qu'un problème est bien cerné. Les journalistes n'ont guère tardé pour s'approprier cette méthode qui a traversé les temps. C'est un tort de ne pas l'exploiter plus souvent en entreprise, et pas uniquement dans le domaine de la qualité tant elle est efficace.
Le lean "par le bas": Et si on mettait en veilleuse le mépris le temps du projet ?
Quasiment tous les projets d'organisation industrielle sont déployés selon un modèle "Top-->down", du haut vers le bas.
Quelle que soit la qualité de l'étude de terrain réalisée, "l'état des lieux", les consultants en charge de la mission n'affichent en règle générale qu'un seul objectif :
Déployer la méthode telle qu'ils la maîtrisent. Point.
Et peu importe : les spécificités de l'entreprise, les ressources potentiellement à développer (et les travers à éliminer) et surtout ne pas tenir compte de
l'avis des gens qui sont sur le terrain et connaissent parfaitement leur environnement avec ses contraintes et ses opportunités, avec lesquels ils jonglent pour construire la valeur.
Trois bémols pour mieux saisir la portée de ce propos
- Premier bémol : Il faut les comprendre. Sous la pression de leur cabinet qui a ses propres objectifs chiffrés, ils n'ont guère le temps ni la latitude de se préoccuper des spécificités des entreprises à réorganiser, quitte à passer à côté d'avantages concurrentiels potentiels.
- Deuxième bémol : les dirigeants d'entreprise n'ont bien trop souvent en ligne de mire que l'accroissement de la productivité. Si on leur faire miroiter les avantages d'une réorganisation miracle rapidement rentabilisée, ils ne se font pas tirer l'oreille plus longtemps. Bon après il y a la concurrence vous expliqueront-ils... Après étude, l'argument à bien souvent bon dos.
- Troisième bémol : Bien évidemment, tous les consultants n'agissent pas ainsi. Pour les plus chevronnés, indépendants ou membres de cabinets à taille humaine, la conscience professionnelle est le principe fondamental de la démarche engagée. Cela dit, ils ne vous vendront pas la lune au désespoir de certains dirigeants et l'ont rejoint le deuxième bémol. Voir aussi ici la catégorisation des consultants et là choisir un consultant
Alors, comment faire ?
Il n'existe que deux approches : soit on impose, c'est la démarche directive, soit on discute et c'est la démarche coopérative.
Légende : projet organisation industrielle : démarche directive ou démarche coopérative ?
Les 5 S pour tout le monde ? Mais non !
Allez un exemple. En discutant, en partageant, on essayant de comprendre comment les gens travaillent, on découvre alors que par exemple les 5 S ne sont pas toujours opportuns. L'ordre strict, la rigueur, tout cela c'est bien. On pourrait parler d'un atelier de réparation ou d'une salle d'opération qui n'ont pas attendu le Lean pour organiser leur espace de travail. Cependant, il est aussi parfois et même souvent préférable de
laisser la liberté au salarié, créateur de valeurs par définition, d'organiser son poste de travail comme il l'entend pour produire plus efficacement.
Les salariés ne sont pas (encore) des robots. Il est tellement plus efficace justement de soutenir les différentes personnalités que de chercher à standardiser les comportements au mépris de ce qui fait de nous un humain.
Exploitons les ressources du Kaizen en dehors des ridelles de la quête de productivité
Il est tout aussi absurde de limiter le Kaizen à la recherche de standardisation dans l'unique optique des gains de productivité. Le Kaizen est aussi un outil extraordinaire pour développer le bien-être en entreprise et rendre la vie meilleure pour les salariés qui sont, on l'oublie trop souvent, non pas un coût, mais bien les créateurs de valeurs et de richesse de l'entreprise. La gestion comptable des salariés les rangeants dans la mauvaise colonne du compte de résultats (celle des charges) est une véritable plaie.
Parvenu à ce stade, on peut alors commencer à réfléchir sérieusement (il serait temps !) à considérer à sa juste valeur les apports de tous les membres de l'entreprise sans se référer à des règles d'autoritarisme totalement anachroniques.
C'est d'ailleurs l'objet de l'ouvrage ci-dessous.
De la démocratie en entreprise
Il est plutôt paradoxal qu'au vingt-et-unième siècle le monde de l'entreprise pratique encore un cloisonnement autoritaire et sans concession entre une direction s'octroyant un pouvoir exclusif et des salariés, pourtant créateurs de valeurs, assujettis aux directives imposées. Pourtant, ne serait-ce que du point de vue économique, en un contexte exacerbé comme le notre il serait peut-être temps de considérer ceux qui font marcher l'entreprise comme des partenaires à part entière.
La démarche proposée dans cet ouvrage se déroule en trois temps :
- Temps 1: décliner le lean management (ou toutes autres méthodes organisationnelles) en étroite coopération avec ceux qui devront l'utiliser au quotidien. Il ne s'agit plus de subir. C'est aussi vrai pour les 30 outils Lean présentés ici. Les mettre en oeuvre en coopération est un gage de succès.
- Temps 2: Exploiter les ressources du Kaizen pour une nouvelle définition de la notion de performance bien plus large, intégrant au premier plan le bien-être de tous (c'est non seulement possible mais nécessaire).
- Temps 3: Construire en dix temps une parfaite coopération de tous (sans blabla, du concret !)
- Sources, références et bibliographie commentés.
La transformation démocratique de l'entreprise
Pour en finir avec le mépris, principe délétère du management d'hier et d'aujourd'hui
Alain Fernandez
Editeur : Mimismo
Pages : 350 pages
Prix : 19,90 Euros
EAN : 978-2959320422
Voir ce livre :
Autres librairies en ligne...

Lire aussi :
Réaliser les projets d'entreprise en coopération...
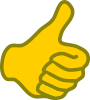
En prime avec ce livre, gratuitement et réservé aux lecteurs,
l'ebook "le dictionnaire du lean" au format pdf.
Faciliter la prise de décision à tous les niveaux
Ce qui importe, c'est de répartir un peu plus le pouvoir et de décentraliser la prise de décision au plus près du terrain, là où se trouve l'information, là où l'action est possible. Encore faut-il réformer la
"mesure de la performance" pour qu'elle soit au service des décideurs et non des gendarmes de l'entreprise.
Ensuite, il est aussi nécessaire de faciliter l'indispensable
"prise de décision en équipe", qui est, quelque part, la clé d'un Lean Management modernisé et pleinement assumé. C'est là l'objet de ce livre avec la méthode SOCRIDE, expliquée et illustrée de cas concret.
- Partie 1: Réformer la mesure de la performance pour qu'elle soit un instrument de progrès et d'aide à la décision pour tous et non plus un absurde instrument de compétition individuelle.
- Partie 2: 7 étapes (SOCRIDE) pour mettre en oeuvre une prise de décision en équipe pleinement assumée.
Quand les équipes de terrain s'engagent et prennent les décisions responsables : la méthode SOCRIDE
Alain Fernandez
Editeur : Eyrolles
Pages : 320 pages
Prix : 25 Euros
EAN : 978-2212569285
Pour acheter ce livre :
L’auteur
Alain Fernandez Consultant et formateur de longue date en France et à l'international, auteur de plusieurs livres publiés aux Éditions Eyrolles consacrés à la réforme de la mesure de la performance pour qu'elle soit une aide à la décision pour tous et aux équipes autonomes et responsables (méthodes Gimsi ® et Socride). Plusieurs de ses livres se sont vendus à plusieurs dizaines de milliers d'exemplaires et sont régulièrement réédités.
Son dernier ouvrage, fondé sur plus de dix ans d'études auprès de coopératives essentiellement, expose une réforme concrète et profonde du management afin de faire entrer la démocratie dans l'entreprise.
Ressources web
Voir aussi...
Partagez cet article...
(total partages cumulés > 145)