Juste à Temps en production, le coeur du système Toyota et du Lean Management
Le Juste à Temps marque un tournant majeur dans l’organisation de la production industrielle. Il ne s’agit plus de planifier la production en se fondant sur des prévisions de ventes, mais bien de réorganiser le flux de production afin de ne fabriquer que ce qui est demandé par le client au juste moment, pour une livraison à la date prévue et acceptée par le client. Voyons tout cela ainsi qu'une critique constructive du Juste à Temps (JAT) pour se souvenir que les extrémistes de la radicalité sont toujours dans l'erreur et une présentation du "Slack" qui propose de mettre un peu de mou dans les rouages.
Pour la fabrication sur prévision, on parle de flux poussé. On pousse le flux vers le marché. Pour la fabrication sur commandes clients en Juste à Temps, on parle de flux tiré. La fabrication est tirée par le marché.
Définition du "Juste à Temps" JAT
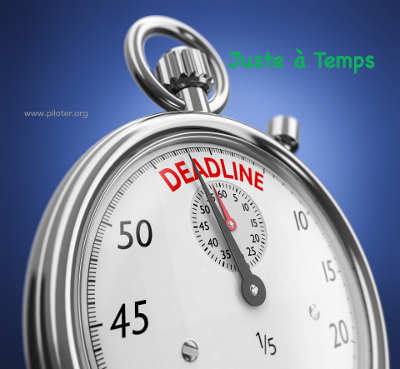
Le Juste à Temps développé au sein des usines Toyota, pilier principal du toyotisme et par conséquent composant clé du Lean Management, n’a d’autre but que celui de réduire au maximum le délai de fabrication entre la prise de commande et la livraison chez le client tout en assurant une maîtrise des coûts.
Autrement dit, il s'agit de fabriquer uniquement ce qu'il faut (pour le client et pas sur stock) quand il le faut (ni trop tôt ni trop tard).
Pour cela, l’idée d’inverser le déclenchement de la production mise en oeuvre par
Taiichi Ohno peut être qualifiée de révolutionnaire, dans le contexte de la production industrielle, bien entendu.
Précision historique
Plus précisément,
Kiichiro Toyoda, fils du fondateur de la dynastie Toyota, et initiateur du virage automobile, aurait bâti les fondations du Juste à Temps dès le démarrage de la nouvelle usine en 1938 (Koromo Plant).
Le tout premier véhicule de la marque Toyoda (qui ne s'appelait pas encore Toyota), le
modèle AA était sorti juste deux années au paravant.
Sources : Le "Toyota Commemorative Museum of Industry of Technology" Nagoya Japan, visité en mai 2024.
Principe du Juste à Temps
Le Juste à temps est une réforme des modes de production classique, il s'agit de passer
du flux poussé au flux tiré.
1. Les produits sont "poussés" vers le marché
Pour le dire vite, le principe de production classique est fondé sur la règle "on fabrique avant de vendre". Les ordres de fabrication sont établis selon des prévisions plus ou moins précises de vente, et la fabrication est lancée pour constituer les stocks d'articles qui seront ensuite vendus au client. Voir ici le principe MRP & MRP2.
2. Les produits sont "tirés" par le marché
-
Le principe du Juste à Temps, symbolisé par le sigle JAT (JIT Just In Time en anglais), est lui fondé sur la règle "on vend avant de fabriquer". Les ordres de fabrication sont lancés au fur et à mesure des commandes clients.
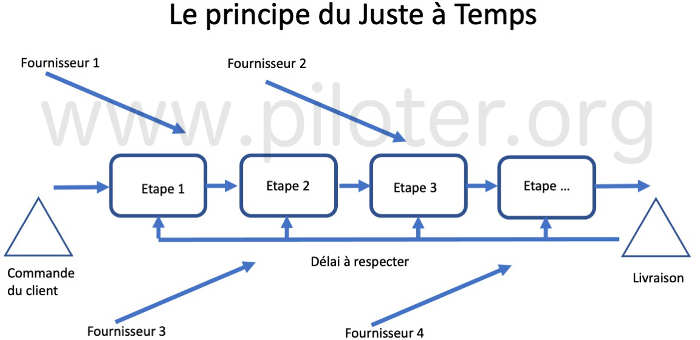
Légende : Le principe du Juste à Temps, la fabrication est déclenchée par les commandes clients, les délais limites de chaque étape de la fabrication sont fixés à rebours selon la date de livraison prévue. Les fournisseurs et sous-traitants sont pleinement impliqués.

Le Juste à Temps est un peu la révolution copernicienne du monde de l'organisation industrielle de la production de masse. Taiichi Ohno disait de lui-même
"qu'il aimait penser à l'envers". C'est tout à fait ce qu'il a su faire au sein d'un industrie dominée par les méthodes du fordisme devenues alors obsolètes face à l'évolution de la demande.
Méthode Juste à Temps en 6 étapes
Comment le mettre en oeuvre ?
Basculer aussi radicalement un système de production ne se fera pas en un jour. Une telle réorganisation exige un changement idéologique radical et le terme n'est pas trop fort, tant s'en faut.
Il s'agit de fluidifier du mieux possible le ou les processus concernés.
Parcourons les six thèmes majeurs de la démarche :
1. Réduction des stocks
Dans le cadre du processus de production, objet de cette étude, l'une des actions fondamentales sera de se focaliser sur les stocks qui devront être réduits à leur plus simple expression. L'objectif idéal dans le cadre du JAT étant de supprimer les stocks en matières premières, semi-finis et produits finis. Le bénéfice théorique est double : on réduit les coûts d'immobilisation et l'on met en évidence les points faibles du flux. On peut alors solutionner les irrégularités qui nuisent à la fluidité.
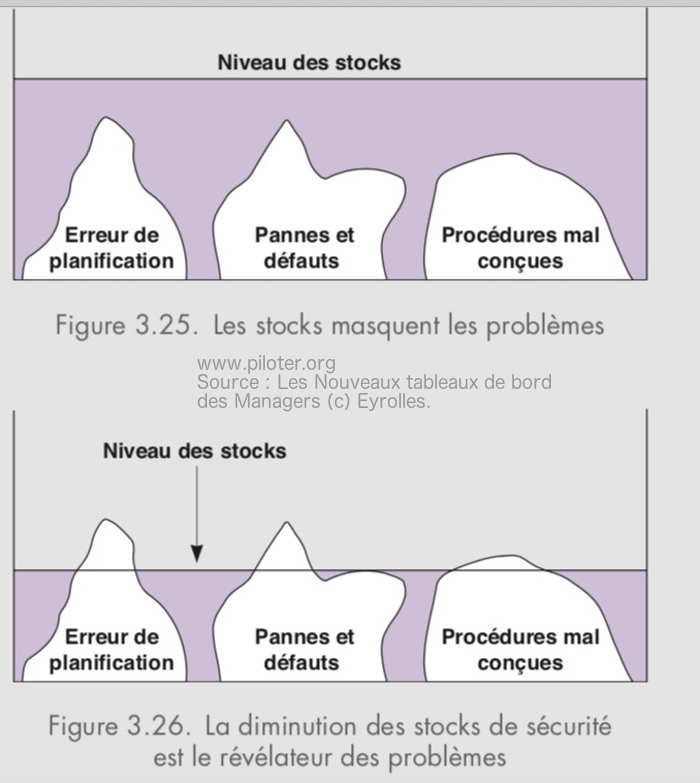
Légende : Les stocks intermédiaires de fournitures ou de produits finis sont utiles pour éviter les ruptures de flux. Mais par voie de conséquence, ils masquent les dysfonctionnements chroniques des processus.
Source de l'illustration : "Les nouveaux tableaux de bord des managers" © Éditions Eyrolles
2. Standardisation poussée
La standardisation des procédures poussée à son extrême est aussi l'une des règles du Juste à Temps, et plus généralement du Toyotisme et de son héritier le Lean Management. Conforme aux lois du Taylorisme, chaque tâche est optimisée afin de perdre le moins de temps possible.
3. Élimination en continu des erreurs
Tous les dysfonctionnement potentiels qui pourraient nuire autant à la fluidité du processus qu'à la qualité des produits délivrés doivent être identifiés en l'instant et résolus sans délai. C'est là le principe du Jidoka.
4. Petites séries
Le Juste à Temps est devenu la solution indispensable pour rester en phase avec les attentes des clients. Si, selon la légende, Henri Ford disait que le client avait le choix de la couleur du véhicule acheté à la condition que celle-ci fusse le noir, un tel autoritarisme commercial est désormais révolu. Le client souhaite acheter des produits personnalisés, et c'est d'autant plus vrai en ce qui concerne le marché automobile.
Il s'agit donc de fournir des véhicules avec suffisamment d'options pour que le client puisse le configurer au moment de la commande selon ses désirs. Pour parvenir à cet objectif, il est impératif de savoir gérer des séries courtes. Or, le changement de série est coûteux en temps. C'est bien pour cela que la production plus classique privilégie les séries longues. Il existe cependant des méthodes comme le SMED pour accélérer les réglages et permettre ainsi une lotification mieux adaptée aux besoins.
5. Maîtrise des cycles
Pour livrer un produit à temps, c'est-à-dire selon le délai proposé et accepté par le client, toutes les étapes du processus doivent être temporellement ajustées pour qu'au final, le temps global corresponde à l'objectif. On parle alors de Takt Time. L'optimal étant atteint lorsque le Temps de cycle, le temps réel d'exécution d'une tâche précise, est équivalent au Takt time qui représente le temps idéal de traitement au sens du délai client.
C'est aussi là que commence l'enfer dans bien des industries. Il ne s'agit plus de réaliser sa tâche correctement en accord avec les procédures et les exigences qualités, mais bien de se mettre tout seul la pression pour respecter le délai client. Vite, toujours plus vite... Avec la course à la réduction des coûts, qui se traduit systématiquement par une réduction des effectifs, nul besoin de faire preuve d'une grande imagination pour comprendre le calvaire quotidien vécu par les indispensables "derniers de corvée" de l'industrie.
Voir aussi Comment augmenter les cadences de production.
6. Kanban
Le Juste à Temps est indissociable de la méthode Kanban développée et industrialisée chez Toyota. Le kanban est une étiquette informative qui permet d'établir un système d'échanges "client/fournisseur" entre les différents postes du processus de fabrication, en partant de l'aval vers le l'amont.
Ce thème bien qu'indissociable du JAT mérite d'être traité plus à fond et fait l'objet d'un article indépendant :
Kanban .
Critique du juste à Temps
Les gains financiers théoriquement significatifs, liés à la mise en oeuvre d'une organisation de Juste à Temps stricto sensu, méritent d'être mis en balance avec l'inévitable pression sur les salariés, les fournisseurs et les sous-traitants.
La loi du chronomètre associée à la chasse aux coûts systématique, autre fondement du toyotisme, ôte le peu de degré de liberté dont disposent les ouvriers placés au "front" de la production.
D'autre part, le travail plus que jamais parcellisé et hyper standardisé est nécessairement cause de troubles musculo-squelettiques et de désintérêt total, connus comme un facteur majeur de dépression.
Pourquoi la productivité devrait toujours être aux dépens des travailleurs qui créent la valeur ? C'est aussi cela le prix du Lean management. Voir ici les
causes d'échec, puisqu'il faut bien appeler les choses par leur nom.
Enfin, malgré les convictions de ses prosélytes les plus enthousiastes, le Juste à Temps ne fonctionne pas pour tous les types de production. Les productions en série relativement courtes de produits à courte vie ne pourront jamais entrer dans le cadre du Lean qui n'a d'autre objectif de figer les processus pour en améliorer l'efficience. Il est bon de se rappeler que l'industrie ne fabrique pas que des automobiles. Voir ici les limites du lean management.
Le Slack
Ou l'art et la manière de mettre un peu de souplesse au sein même de processus trop rigides...
Le Slack en organisation industrielle propose de réserver quelques ressources supplémentaires disponibles en permanence afin d’absorber les soubresauts et autres aléas que connaît toutes productions, même les moins complexes.
En substance, il s’agit de modérer un tant soit peu l’obsession de l’optimisation extrême de la théorie des flux tendus prise à la lettre et assurer notamment une gestion des stocks moins radicale.
Les plus fervents défenseurs du Lean nous objecteront que ce matelas amortisseur des coups durs n’est autre qu’une forme de « gaspillage » puisqu’il « suffit » de supprimer les irrégularités de la production comme le préconise la démarche Lean (Mura et Heijunka).

Le type de gaspillage
Mura correspond peu ou prou à toutes les irrégularités du flux.
Heijiunka est une méthode de lissage dans la durée des flux de production sans être (trop) tributaire des à-coups de commandes.
Pour les inciter à relativiser leur jugement, on ne saura que trop leur conseiller de descendre dans l’arène et de passer du temps avec ceux qui sont au charbon et qui créent concrètement la valeur. Ils comprendront rapidement que la réalité n’est pas aussi simple qu’une modélisation des processus aussi soignée soit-elle, et que rien n’est parfait dans ce bas monde. En référence à
Edgar Morin, nous vivons dans un monde d’incertitudes. Rationaliser, c’est se rassurer, c’est chercher des ilots de certitudes pour se reposer l’esprit. Mais, ça ce n’est pas réaliste !
Richard Cyert and James March A Behavioral Theory of the Firm 1963 Wiley.
Parmi les thèmes développés dans cet ouvrage majeur qui servit de base à de nombreux travaux (March & Olsen notamment), les auteurs étudient le concept de Slack désignant les ressources excédentaires, qu’elles soient budgétaires ou organisationnelles, qui permettent à l’entreprise d’assurer son fonctionnement. En effet, selon les auteurs, une organisation est toujours en état d’instabilité en raison des multiples groupes de pression, des limites du
processus de décision et des conflits résultants. C’est grâce à la disponibilité de ces ressources non optimisées que l’organisation parvient à atteindre ses objectifs et à innover le cas échéant.
Les limites de la réduction des stocks
Si la suppression des stocks est une bonne solution pour fluidifier les processus, tout en mettant en évidence les défauts, elle devient rapidement une difficulté majeure lorsque la production n'est pas régulière ou qu'un dysfonctionnement, imprévu par définition, ne manquera pas de survenir.
La réduction des stocks ne doit pas devenir une obsession (en contrepoint du lean pur et dur). Les stocks sont utiles pour réguler le flux si besoin, sans appliquer pour autant une pression infernale sur les épaules des salariés concernés. Luc Boltanski et Ève Chiapello notaient dans leur ouvrage majeur (Le nouvel esprit du capitalisme) que la suppression des stocks était surtout le moyen de faire supporterx la charge de la demande (du client donc) au sein même des ateliers. Satoshi Kamata effectuait la même constatation non pas du point de vue externe du sociologue mais bien celui de l'ouvrier sur la chaîne de production de Toyota (L'usine du désespoir").
Les limites de la réduction des temps de cycle
La question se pose dans les mêmes termes pour la réduction drastique des temps de cycles avec le spectre du
Takt time en perspective.
Il est facile de supprimer les temps improductifs. Les Temps d'échanges, de discussions, les déplacements n'apportent rien directement au processus de création de valeurs.

Sauf qu'en substance, disposer d'un peu de marge de manoeuvre permet de régler les inévitables aléas, tout en ne transformant pas un poste de travail en un enfer sur terre.
Un peu de marge, de souplesse
Il en est de même pour l'exploitation des ressources physiques à pleine capacité. Il n'est jamais recommandé d'exploiter en permanence un équipement à sa limite sans se laisser une marge de manoeuvre, c'est une vérité première.
Bref, laisser un peu de marge, que ce soit dans les stocks, dans les temps de travail et dans les capacités des ressources, c'est le moyen de construire des unités de production un peu plus humaines et sûrement plus efficaces dans la durée. C'est un peu cela que l'on appelle "Slack" en opposition directe à un Lean Management pris au pied de la lettre.
Flux poussé, MRP MRP2
Le frère ennemi du Juste à Temps, les flux tirés, est justement le mode de fonctionnement plus classique en flux poussé.
Au contraire du juste à Temps, où la fabrication est lancée selon les commandes clients, le principe classique du flux poussé est fondé sur une fabrication sur prévisions des ventes.
Les besoins du marché sont estimés à un horizon compatible avec les processus de fabrication, et les ordres de fabrication adéquats sont lancés en conséquence afin d’être en mesure de répondre aux commandes des clients. Plus simplement, on produit sur stock et l'on sert les commandes clients à partir du stock. Pour garantir la fluidité des processus, on crée aussi des stocks intermédiaires. Grâce à ces stocks, on se protège aussi des irrégularités de livraisons et de disponibilités des fournisseurs et des sous-traitants.
Le stock
Un stock coûte. Qu’il s'agisse de produits finis, semi-finis ou de matières premières, un stock représente un coût loin d'être négligeable. C’est une immobilisation financière conséquente. Quoi qu'il en soit, la
gestion des stocks n’est pas une mince affaire.
Voyons maintenant les deux principaux systèmes d'ordonnancement de la production à flux poussé MRP et MRP2 :
MRP : Materials Requirement Planning
Le principe le plus simple (en apparence) pour planifier et ordonnancer les fabrications en ne tenant compte que des besoins, en partant d’un principe d’une disponibilité infinie des ressources disponibles.
Comme tout ne s'oppose pas vraiment, il peut être judicieux pour certains types de production de combiner un système de gestion de la production MRP avec le Kanban. Le MRP permet d'anticiper les besoins sur prévisions, et le système Kanban est utilisé pour réaliser les produits finis à la demande.
MRP expliqué sur la wikipedia anglophone
MRP2 : Manufacturing resource planning (MRP II)
Là, il s’agit de tenir compte de la capabilité des ressources disponibles. Le calcul est plus fin que précédemment. Les
outils d’ERP Enterprise Ressource Planning pour leur module « Production » intègrent les outils nécessaires pour les indispensables calculs de production, comme tout bon outil de
Gestion de Production (GPAO).
MRP2 expliqué sur la wikipedia anglophone
De la démocratie et de la coopération pour mieux réussir les projets organisationnels
Le Juste à Temps n'est pas la méthode miracle que l'on peut implanter telle qu'elle sans se préoccuper des spécificités de la production et des attentes des clients. Une méthode ça s'adapte. Pour cela encore faut-il faire confiance (après avoir "donner confiance" au préalable) aux acteurs de terrain, c'est-à-dire ce qui font vivre les processus de production au sens large pour travailler en une réelle coopération. C'est bien ainsi que l'on "fabrique" la meilleure solution. C'est le thème de la première partie du livre ci-après:
La transformation démocratique de l'entreprise
Pour en finir avec le mépris, principe délétère du management d'hier et d'aujourd'hui
Alain Fernandez
Editeur : Mimismo
Pages : 350 pages
Prix : 19,90 Euros
EAN : 978-2959320422
Présentation détaillée du livre "la transformation démocratique de l'entreprise"
Autres librairies en ligne...
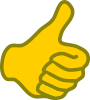
En prime avec ce livre, gratuitement et réservé aux lecteurs,
l'ebook "le dictionnaire du lean" au format pdf.
L’auteur
Alain Fernandez est un spécialiste de la mesure de la performance et de l’aide à la décision. Au fil de ces vingt dernières années, il a conduit et accompagné de nombreux projets d'entreprise en France et à l'International. Il est l'auteur de plusieurs livres publiés aux Éditions Eyrolles consacrés à ce thème et connexes, vendus à plusieurs dizaines de milliers d'exemplaires et régulièrement réédités.
Les sources de l'article
La réussite de tous les projets de ce type repose sur une participation active des équipes de terrain, en charge de prendre des décisions dépassant largement le simple registre procédural. Il s'agit de leur en donner les moyens et de commencer par vérifier son propre système de mesure de la performance. C'est là l'objet de l'ouvrage ci-après...
Les tableaux de bord du manager innovant
Une démarche en 7 étapes pour faciliter la prise de décision en équipe
Alain Fernandez
Éditeur : Eyrolles
Pages : 320 pages
☛ Consultez la fiche technique »»»
Pour acheter ce livre :
Format ebook : PDF & ePub,
Format Kindle
Système Lean
Penser l'entreprise au plus juste
James Womack, Daniel Jones
Pearson Education 2ème édition
464 pages
Dispo :
www.amazon.fr & Format Kindle
Toyota Production System
Beyond Large-Scale Production
Taiichi Ohno
Productivity Press
176 pages (anglais)
Dispo :
www.amazon.fr & Format Kindle
A Study of the Toyota Production System
From an Industrial Engineering Viewpoint
Shigeo Shingo
Productivity Press
296 pages (anglais)
Dispo :
www.amazon.fr & Format Kindle
Voir aussi...
Partagez cet article...
(total partages cumulés > 105)